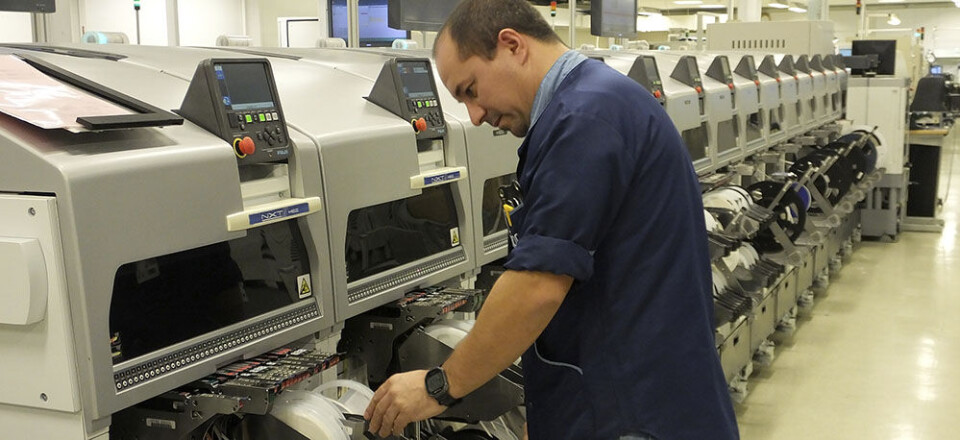
Øst, vest – hjemme best?
Det er blitt diskutert i den senere tid hvorvidt trenden om hjemhenting – «homesourcing» eller «backshoring» – av produksjonstjenester (EMS) faktisk er en trend, om den i så fall er langvarig, og hvordan den eventuelt vil påvirke industrien.
Denne artikkelen er 2 år eller eldre
Internasjonalt har det vært en økende uro den senere tid rundt Kinas dominerende posisjon, ikke bare som produksjonsland, men etterhvert også som teknologisenter innen elektronikkproduksjon. Det gjenspeiles for eksempel i produksjon av mønsterkort, der Europa for noen år siden stod for mer enn 40% av verdens produksjon. I dag er tallet 3%. Mens Kina har gjort seg nærmest uunnværlig med sin andel på 50%, og er ledende innen noen av de mest avanserte mønsterkortteknologiene på markedet.
Større bevissthet
Selv om det er vanskelig å peke på en tydelig trend, hverken i Norge eller Europa for øvrig, virker det å vokse frem en stadig større bevissthet på å holde i hvert fall den kritiske delen av produksjonen – og produksjonskunnskapen – innenfor egne landegrenser. Det er inntrykket vi får når vi snakker med både produkteiere og kontraktsprodusenter.
Og med et par unntak, ser det ut som elektronikkindustrien i Norge gjør det rimelig bra, pandemi og markedsvariasjoner tatt i betraktning.
Back to Norway?
Vi stilte noen produksjonsbedrifter spørsmålet om «homesourcing» som trend, i tilfelle vil det dreie seg mest om «back to Europe», eller også «back to Norway»? – Jeg tror det er begge deler! Men, vi ser en tendens til at produksjon i Norge blir mer og mer et kvalitetsstempel som mange kunder setter større og større pris på, sier adm. direktør Tor Giæver i Hapro. Han får støtte av daglig leder i Axxe, Øystein Back, som tror det er store muligheter for å få mye produksjon tilbake til Norge, men at det muligens vil være vanskelig å «bygge nok kapasitet» på kort varsel. – Kanskje vi endelig får underkapasitet, ler han. Men advarer mot at det samme vil kunne gjelde for tilgang på kompetanse (både høyskole og fagbrev).
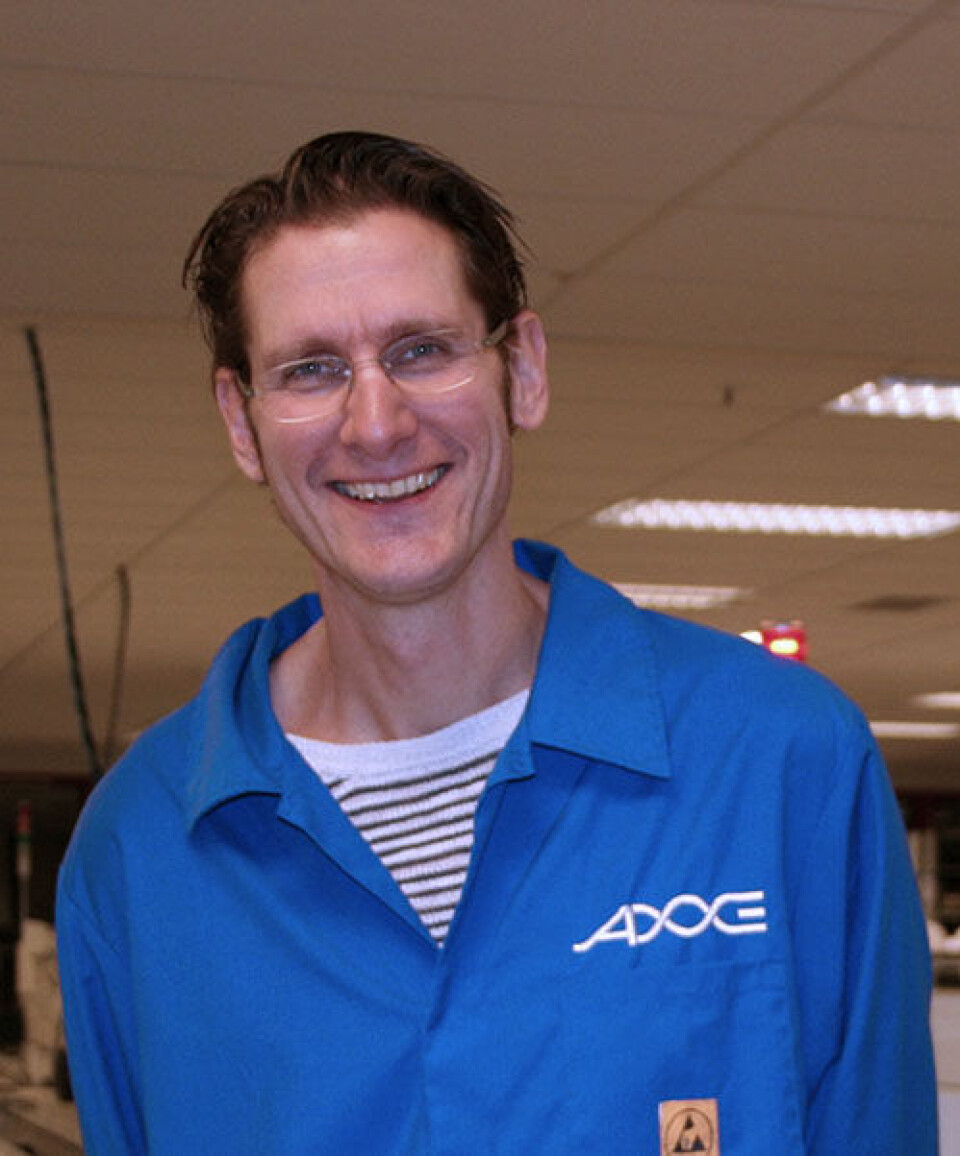
Kina ingen favoritt
– Kina er nok ikke den største favoritten for ny transfer lenger, kommenterer daglig leder Øyvind Sedivy i Norautron tørt. Årsak/sammenheng er selvfølgelig internasjonal politikk, tollsatser, teknologikopiering og lignende, mener Sedivy, som på den annen side ser at Øst-Europa/Baltikum blir mer attraktivt nå. – Vi ser vel at hos de større kundene så er trenden kanskje en tilbake-sourcing til disse områdene i forbindelse med generasjonsskifte på produktene, fremholder han.
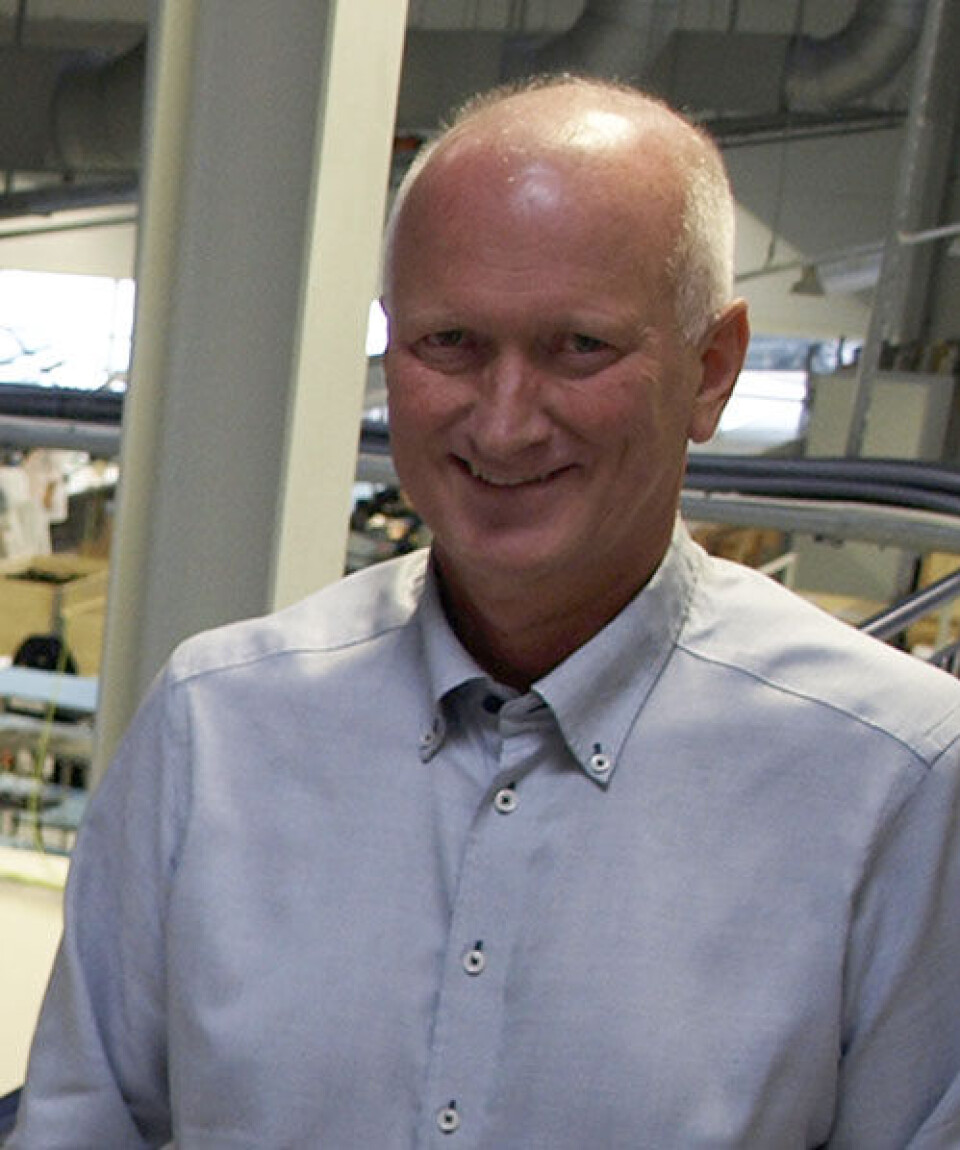
På bakgrunn av kostnader er det fortsatt mest snakk om produksjon av prototyper og pilotserier i Norge, mens serieproduksjon vil finne sted fortrinnsvis i lavkostland i umiddelbar nærhet, ifølge Sedivy.
Suksessfaktorer?
Men er den norske EMS-industrien rustet til å holde prosjektene innenlands, og hva kan være kritiske faktorer for å lykkes? – Ja, det tror jeg absolutt. Det er stor fart i den norske EMS-industrien og de fleste produsenter opplever sterk vekst. Eksempel på kritiske faktorer er at vi må være konkurransedyktige siden vi er globalt konkurranseutsatt, og at den norske kvaliteten og påliteligheten blir verdsatt, påpeker Giæver.
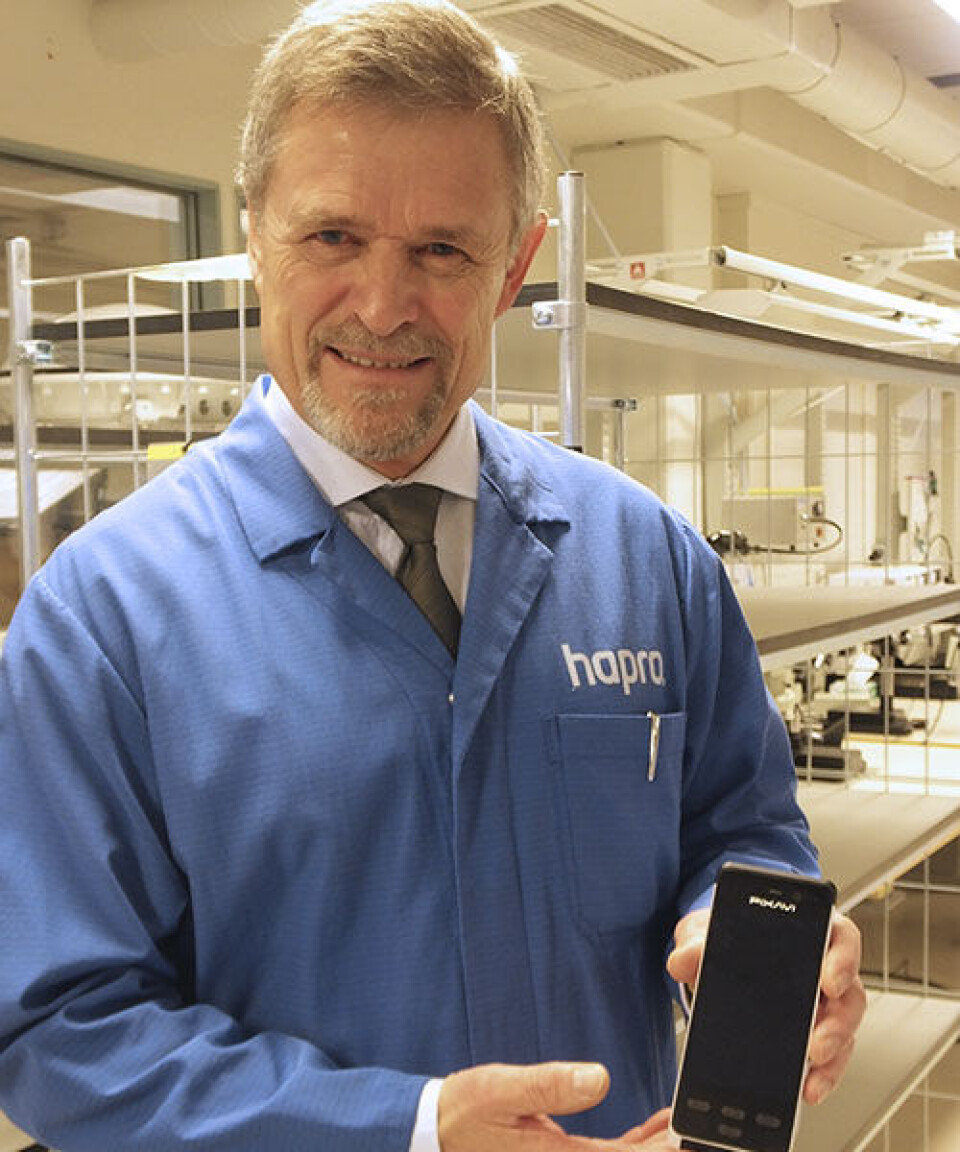
«Hi end, hi cost»
– Vi er uten tvil rustet til å ta vare på «high end, high tech og high cost» produkter som ikke har større volum. Her blir gjerne Norge mer kostnadseffektivt pga. seriestørrelser, kompleksitet og evne til å snu seg rundt vesentlig raskere, mener Sedivy. – Jo mer håndarbeid (kabler, spesiell mekanikk, etc), jo vanskeligere er det. På den annen side blir roboter og kamerasystemer bedre «dag for dag». Det er viktig med samarbeid mellom oppdragsgiver, fabrikk og forskning. Her tror jeg svenskene er noen hestehoder foran – mye vi kan lære der, kommenterer Back.
Kvalitet
Kvalitet er også en faktor, noe alle er enige om. For eksempel kan Norautron legge frem kvalitetsstatistikk som for volumprodukt i antall 50k er på 0,0028% yield. – Og da er kundens designfeil, programvarefeil og installasjonsfeil tatt med, i tillegg til komponentfeil og workmanship, opplyser Sedivy.
Made in Norway
– Det finnes også kunder som er maskinvaresensitive som ikke vil ut av Norge (Skandinavia) av frykt for egen teknologi. I tillegg finnes det kunder som skal brande med Made in Norway, selv i norsk sammenheng i høyt volum, understreker Sedivy. – Min oppfatning er at i alle fall de største aktørene er rustet både finansielt og teknologisk til å ta denne typen produksjon i Norge, sier han.
Design for produksjon/test
Er det noen grep elektronikkutviklerne/-designerne eventuelt kan gjøre for å øke mulighetene for lokal produksjon? – Selvfølgelig tenke DFM/DFT (design for manufacturing/design for test, red. anm.) og for mest mulig automatikk for å holde prosesstider og kost nede. I tillegg må de som kjøper inn være villig til å se total cost of product, ikke bare deler av kosten mht. eget tidsforbruk, frakt, tidsforskjeller osv., sier Sedivy.
Tidlig dialog
Back på sin side peker på at det er avgjørende med tidlig dialog! – Oppdragsgiver må se på fabrikken «som sin egen» og behandle dem som kollegaer som inkluderes i prosjektene. Man må i større grad se på fabrikken som en viktig ressurs og partner, fremholder han. – Dette kan vanskeliggjøre typiske «priskonkurranser» som innkjøpere er glad i, men alt for mange «tegner på bakrommet» og sender ut til mange for å presse pris. Ofte ender man opp med høyere pris, lavere kvalitet og, dersom man ender opp i utlandet, høyere risiko, påpeker Back.
Tett samarbeid!
Giæver er hjertens enig på dette springende punkt: – Her tror jeg bestemt at nærhet og integrert samarbeid mellom produktutvikling og produsent er helt avgjørende, sier han. – Dette bidrar til produkter blir designet for effektiv produksjon og effektiv test, og at industrialiseringen derfor vil gå mye raskere, understreker Giæver.
De tre produksjonsbedriftene vi har snakket med her, melder alle om forventet vekst i 2021.