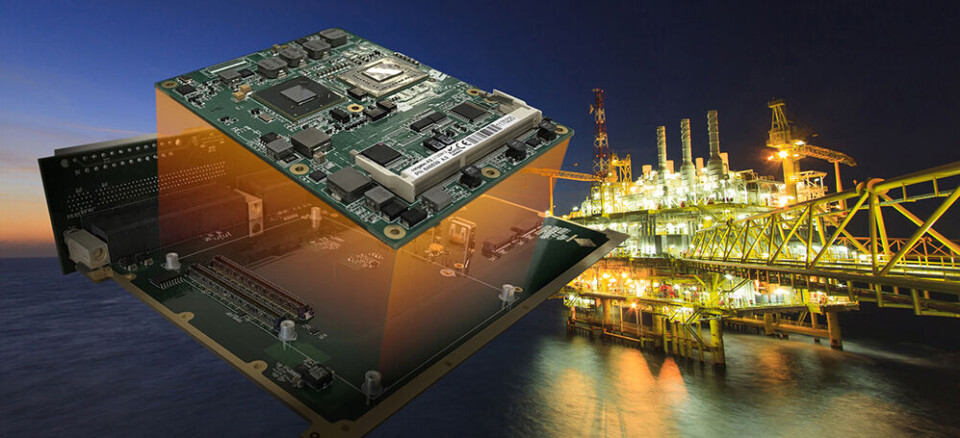
Backplane system designs rely more and more on Computer-on-Modules for CPU integration COMs for CompactPCI Serial, VPX or VME
Backplane systems such as CompactPCI Serial or VPX and VME have a substantial market share in embedded computing. Their high design flexibility makes them attractive for the prospering rugged edge computing market in various industries. Adding Computer-on-Modules to that design principle makes them even more versatile.
Denne artikkelen er 2 år eller eldre
Engineers have long been embracing an embedded system design concept that enables them to configure a dedicated platform by simply plugging various boards into a system. The first embedded computers of that kind were built in the last millennium on AT/ISA96 by companies such as Siemens, and with support from standardization bodies such as PICMG and VITA, the backplane system approach paved its way into many different markets, from aerospace, governmental computing and defense, to transportation, industrial automation, broadcasting and carrier-grade telecommunications. In 2018, the plug-in boards for backplane systems made up approximately 33% of the entire embedded board market. The system integration market had nearly the same size, accounting for approximately 45% of the entire market of CompactPCI Serial. Analysts also predict growing demand for application-specific adaptations on both the software and the hardware level. System integration and customization services are therefore projected to grow at a lucrative rate of over 12% between 2019 and 20251.
Benefits of the ‘COM & carrier’ approach for SBCs in CompactPCI Serial, VME and VPX systems,The processor board is crucial
While I/O boards are mostly tailored to cater for specific needs – digital I/O boards are for example highly scalable – the CPU board is a critical point of customization. Here, it boils down to the question: Do OEMs want to work with commercial-off-the-shelf (COTS) available standard boards, or do they need a platform that is tailored to their dedicated needs? Often, the standard boards come equipped with a broad spectrum of interfaces. If the end application has only small production lots, it is acceptable to pay for interfaces that are not actually needed. But when larger quantities are involved, it is important to eliminate all unnecessary components. In addition to the cost factor, there are also space-saving considerations: If the CPU board provides only the features that are actually required, the board design – and consequently the entire system – can often be more compact. But is a dedicated variant of a standard board needed under those circumstances? This would mean that each new processor generation would require a new customization, with all the corresponding NRE costs! Inventive system engineers from the integration service market therefore went deeper into the evaluations, and today offer not just system configuration but more and more often also CPU board customization services, utilizing standardized Computer-on-Modules and individually designed carrier boards. For OEM customers, this translates into significant cost savings for the series production of backplane systems such as CompactPCI Serial, VPX and VME.
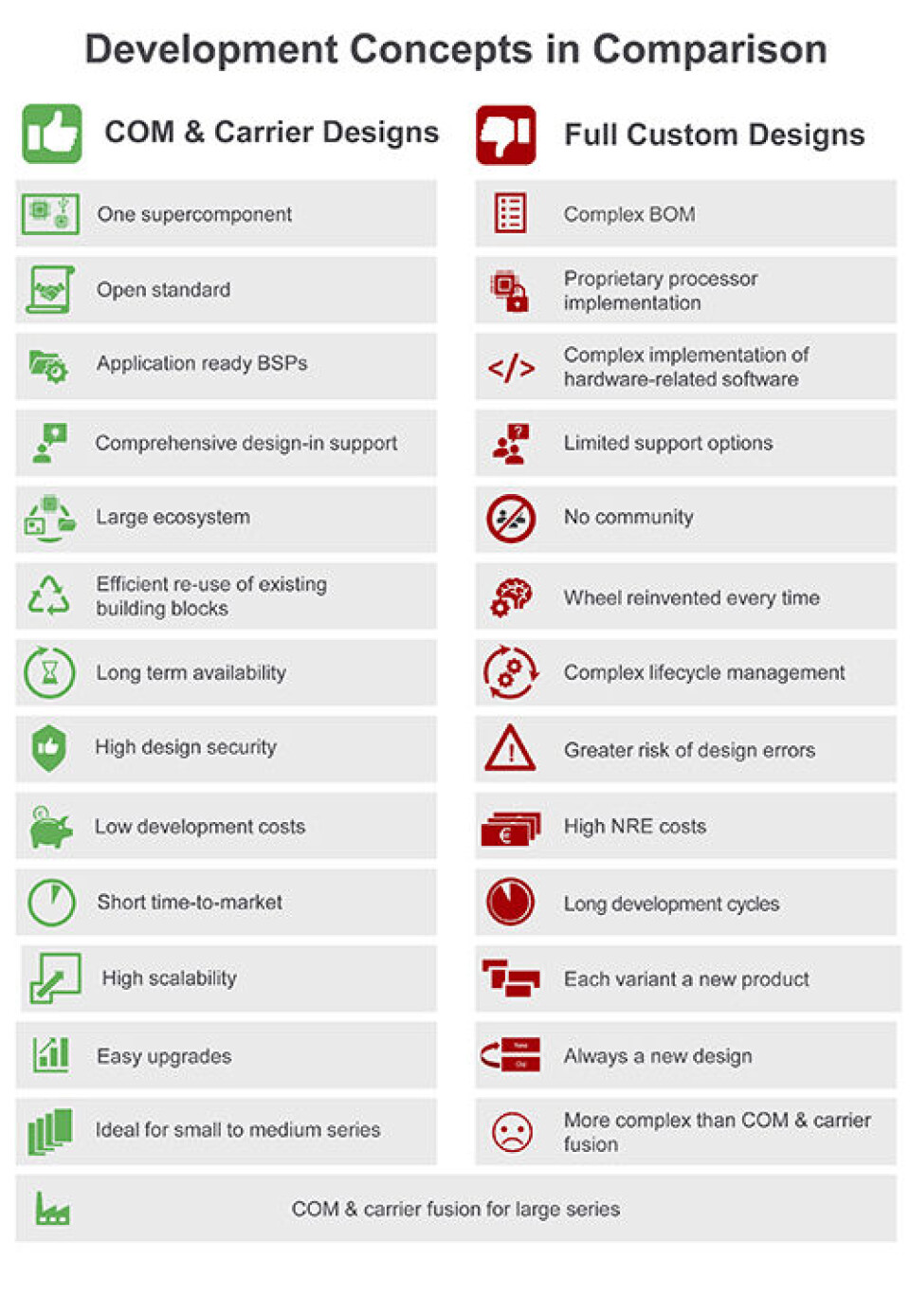
The perfect fit for customer requirements
Computer-on-Modules are admittedly not the best choice when a standard board with an acceptable price tag and only a few surplus interfaces is available. But whenever more customization is needed to create a perfect fit for the OEM application, then the Computer-on-Module and carrier approach gets increasingly attractive for CompactPCI Serial, VPX and VME. This is because such a design can directly support various custom-specific interfaces on the CPU board instead of requiring a dedicated I/O board with the corresponding costs. Another distinct benefit is the fact that the design is not tied to a certain processor setup. This means that the OEM and industrial end user can take the application-specific carrier board and scale the CPU as demanded. This is beneficial for system families and might include a wide TDP range of a single processor family by adopting the cooling; it could be a second source Computer-on-Module vendor for greater independence; and ultimately, it could also be an entirely new generation of processors with different BGA pins. Even scaling across ARM and x86 processors is possible if one utilizes Computer-on-Module standards that support both options.
Better ROI, reduced NRE and improved sustainability
Once such a dedicated carrier has been designed, applications can reside for many years in the same CPU carrier board configuration, providing ultra scalability and longevity over several processor generations. Such designs offer a really great ROI and significantly reduced NRE costs while also being highly sustainable: When a performance update is needed or a processor becomes obsolete, only the module needs to be exchanged; everything else can be re-used. Designers of edge systems for the carrier-grade communication sector have estimated that upgrading a fog server configuration with Computer-on-Modules will cost only 50% of the initial investment for the first performance generation. It is easily understandable that the wastage factor shrinks even more significantly, as approximately 85% of the entire physical hardware can be re-used. This is a real benefit for companies offering, for example, edge computing ‘as a service’, as the sales of entire systems is not their market anymore. It is interesting to see that economic and ecological arguments work hand in hand here, rather than conflicting with each other.
“Together with congatec we can offer OEMs quite cost effective COM & carrier board designs for VME, VPX or CompactPCI Serial,” explains Recab CEO Martin Frederiksen.A joker up system integrators’ sleeves
So why have we not done such system designs earlier? The reason may be that embedded computing vendors with a broad platform portfolio are not interested in the re-use of module form factors on standard embedded motherboards or SBCs. Often, there are different entities responsible for those different designs who compete with each other. But times are changing and some system integration vendors, such as UK-based Recab, are now opening up this opportunity to their OEM customers. The company offers OEMs everything from system integration services to carrier board designs. The only thing they don’t do themselves is to design dedicated CPU boards, preferring to collaborate with leading CPU board vendors in this area instead. Offering long-term expertise in the system integration and customization market for VME, VPX and CompactPCI Serial, Recab is therefore also the right address for getting an answer to the critical question: “Do I need a standard CPU board, a custom variant of this board, or a COM and carrier design for my OEM system?” More and more frequently, the answer is COM and carrier as such designs often meet the specific needs of OEM systems better, while also offering far greater sustainability and ROI in the long term.
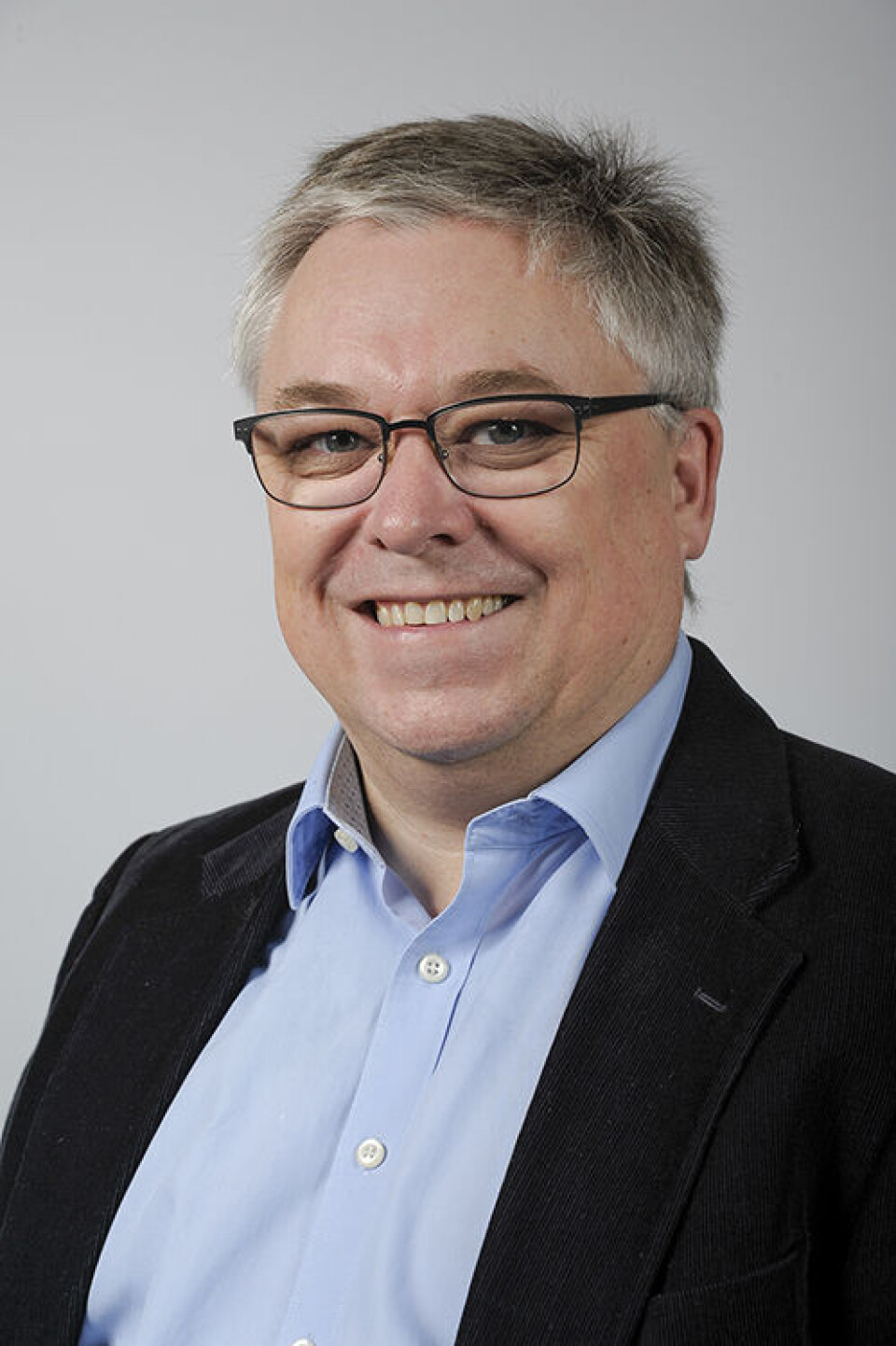
Designed for the edge
Recab has already had such COM and carrier designs in place across various industries for several years. The most recently realized system is a COM Express module on an ultra-rugged carrier tailored for the oil and gas industry, where there is a great need for improved digital transformation both upstream and midstream. Both sectors are characterized by distributed assets and infrastructures in harsh environments and therefore require ultra-robust embedded platforms to address the digital transformation challenge that offers huge cost savings potential. The International Energy Agency estimates that digitization can reduce production costs in the oil and gas sector by up to 20%. According to auditing and consulting firm PwC, there is great potential for savings through more efficient maintenance and better utilization of assets. Further savings potential can be realized in the supply chain, through the use of artificial intelligence and integrated platforms that connect organizations with external partners. By digitizing these processes, companies in the upstream and midstream sector can potentially save up to $1 trillion in capital and operating costs2.
Digitization – a mega market
The new Recab platform is built to realize this potential and meets the requirements of the upstream and midstream oil and gas industry. It is designed for extended temperature ranges, with optional conformal coating to protect against the effects of salt water or condensation caused by large temperature fluctuations. In addition, it offers comprehensive server class RAS (reliability, availability, serviceability) features that enable OEMs to reliably manage thousands of devices remotely. As multicore designs with currently up to 6 cores and a particularly low 25W TDP, the platforms are suitable for completely fanless and therefore maintenance-free 24/7 operation in hermetically sealed housings with the highest IP protection classes. Virtual machines based on RTS hypervisor technologies allow optimal utilization of existing computing resources by partitioning the various tasks – including local real-time control as well as tactile internet. Another benefit of this virtualization option is the fact that these new platforms are also perfect for building cost-efficient universal Customer Premises Equipment (uCPE). Such open standard hardware equipment is used to host telecom network functions at the customers’ edge IT, including Software Defined Networks (SDN) and Network Functions Virtualization (NFV).
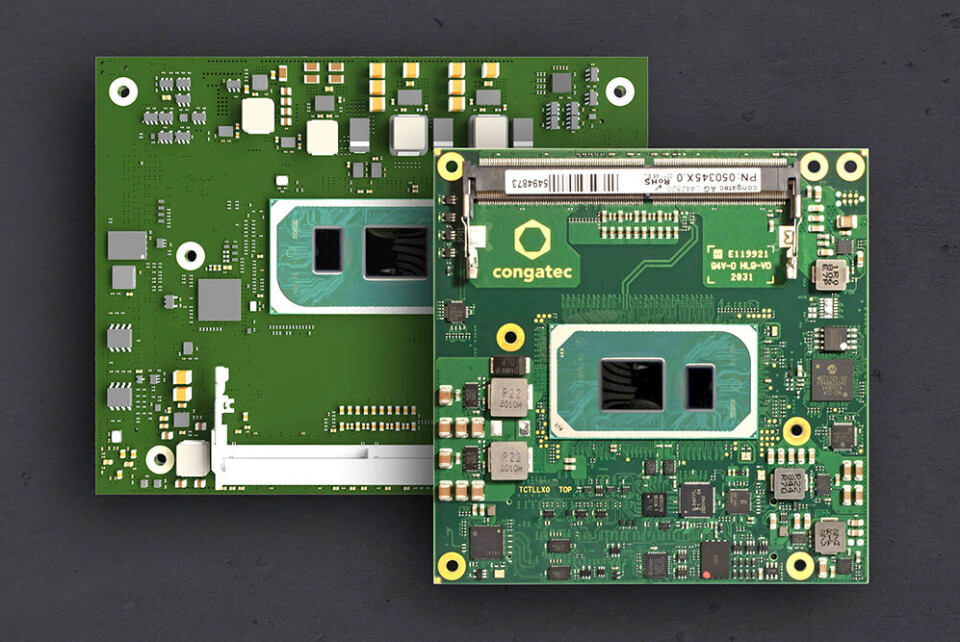
A perfectly integrated solution
For the standard Computer-on-Modules, Recab has chosen congatec as their supplier and partner. This company with headquarters in Germany is leading the worldwide Computer-on-Module market. Setting up the collaboration was made easy by the fact that Recab CEO Martin Frederiksen spent many years looking after congatec sales in the UK and Nordics in his previous career. Leveraging their close relationship with this vendor, Recab positions itself as congatec’s partner to bring COM designs to the market of CompactPCI Serial as well as VPX and VME. It will be interesting to see how many COM-HPC and COM Express standard carriers the company will launch to further improve customer benefits, and how many new markets it will enter which it would never have addressed independently. In short, when evaluating a Computer-on-Module approach for CompactPCI Serial as well as VPX and VM, it is definitely worth checking the offering of congatec’s carrier board design service partner. Actually, this service is also scheduled to become available over the congatec sales channel to further accelerate the reach of this attractive design principle for better ROI and sustainability.
1 See https://www.gminsights.com/industry-analysis/single-board-computer-sbc-market
2 See https://www.strategyand.pwc.com/report/drilling-for-data